Recovered History
The history of a glass factory and its production, recorded in a series of objects that go by the label Recovered.
Inspired by the unique aesthetic qualities of waste produced in glassmaking, the collection transforms residual material into new shapes and meanings, while preserving its distinctive character. The objects in the Recovered and Recovered.history series bear the traces of the singular aesthetics of glass destroyed deliberately, in a controlled manner. The colour scheme is a visual manuscript of the history of glass production at Valner glass making studio.
The collection is a result of three strikingly different processing techniques - three particular approaches to waste material, aiming at a playful and slightly exaggerated shift in the aesthetic perspective of the client - the one who looks, and the producer - the one who creates.
Inspired by the unique aesthetic qualities of waste produced in glassmaking, the collection transforms residual material into new shapes and meanings, while preserving its distinctive character. The objects in the Recovered and Recovered.history series bear the traces of the singular aesthetics of glass destroyed deliberately, in a controlled manner. The colour scheme is a visual manuscript of the history of glass production at Valner glass making studio.
The collection is a result of three strikingly different processing techniques - three particular approaches to waste material, aiming at a playful and slightly exaggerated shift in the aesthetic perspective of the client - the one who looks, and the producer - the one who creates.
Designer.
David Valner
David Valner
Material.
Handcrafted glass
Handcrafted glass
Year.
2018
2018
Unused, strongly stained glass
The so-called “rubies” are used in handwork for colouring and decoration of glass products. It is a strongly coloured stained glass in the form of cylinders, which are used in various production techniques by heating. However, not all of the material is used for processing, and a considerable number of unused pieces is produced in the glassworks within a few years. This residual material is gradually mixed and a simple tool is used to melt several colours together. Due to the different hardness of the individual colours and their chemical reaction, a unique decoration material is created when mixed. This material is placed on the classic crystal glass shapes that are typical for the region where the glassworks resides.
Finished products with defect
The so-called quality inspection is carried out in the glassworks. About 10% of products with various defects, from large bubbles to so-called “stones”, i.e. unmelt pieces of glass raw materials, will not pass this check in case of hand-made custom production. These are almost finished products, but unfortunately, they have to be thrown into a waste container. The use of this material has become the primary inspiration for originally decorated vases. The cold defective product is put back into the mould in which it was created and new hot glass is “blown” into it. Thermal shock will crack the original product and create a unique decor of the new object.
The so-called “rubies” are used in handwork for colouring and decoration of glass products. It is a strongly coloured stained glass in the form of cylinders, which are used in various production techniques by heating. However, not all of the material is used for processing, and a considerable number of unused pieces is produced in the glassworks within a few years. This residual material is gradually mixed and a simple tool is used to melt several colours together. Due to the different hardness of the individual colours and their chemical reaction, a unique decoration material is created when mixed. This material is placed on the classic crystal glass shapes that are typical for the region where the glassworks resides.
Finished products with defect
The so-called quality inspection is carried out in the glassworks. About 10% of products with various defects, from large bubbles to so-called “stones”, i.e. unmelt pieces of glass raw materials, will not pass this check in case of hand-made custom production. These are almost finished products, but unfortunately, they have to be thrown into a waste container. The use of this material has become the primary inspiration for originally decorated vases. The cold defective product is put back into the mould in which it was created and new hot glass is “blown” into it. Thermal shock will crack the original product and create a unique decor of the new object.
Collection
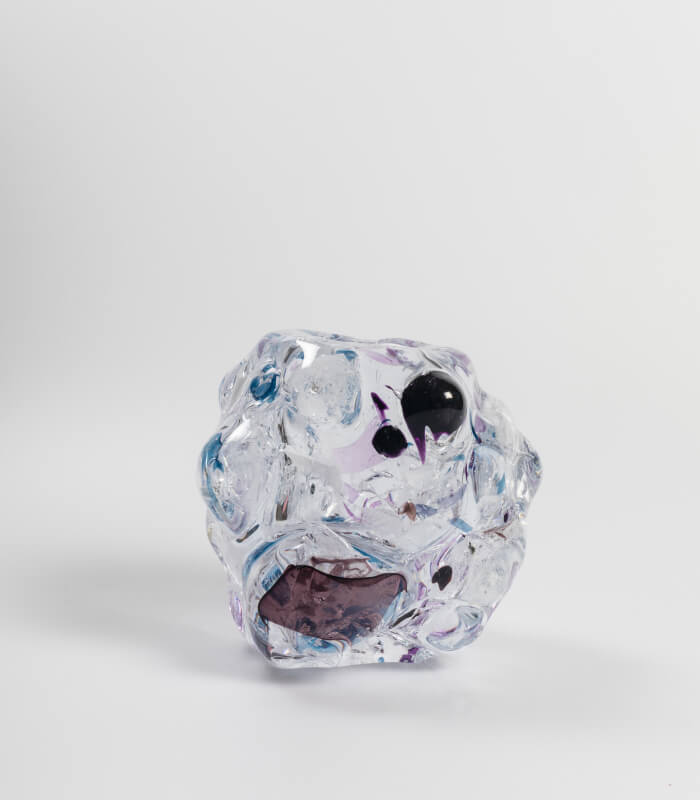


